LIFECYCLE STAGE: MANUFACTURE
Digitally transform your batch and non-batch manufacturing activities to increase production speed and improve product quality
The Manufacture Stage incorporates:
Batch execution
Work-in-progress material handling
Equipment processing
Manufacturing activity modernization
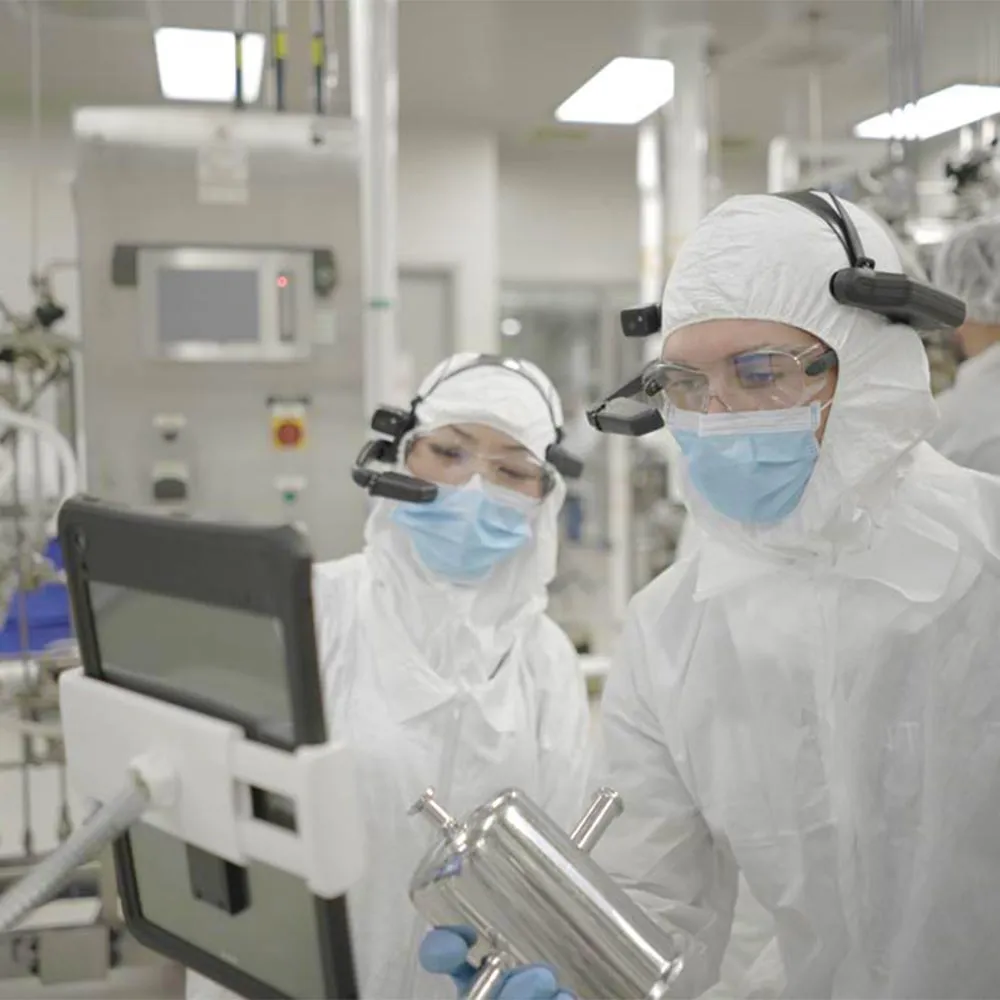
Manufacture Stage use cases
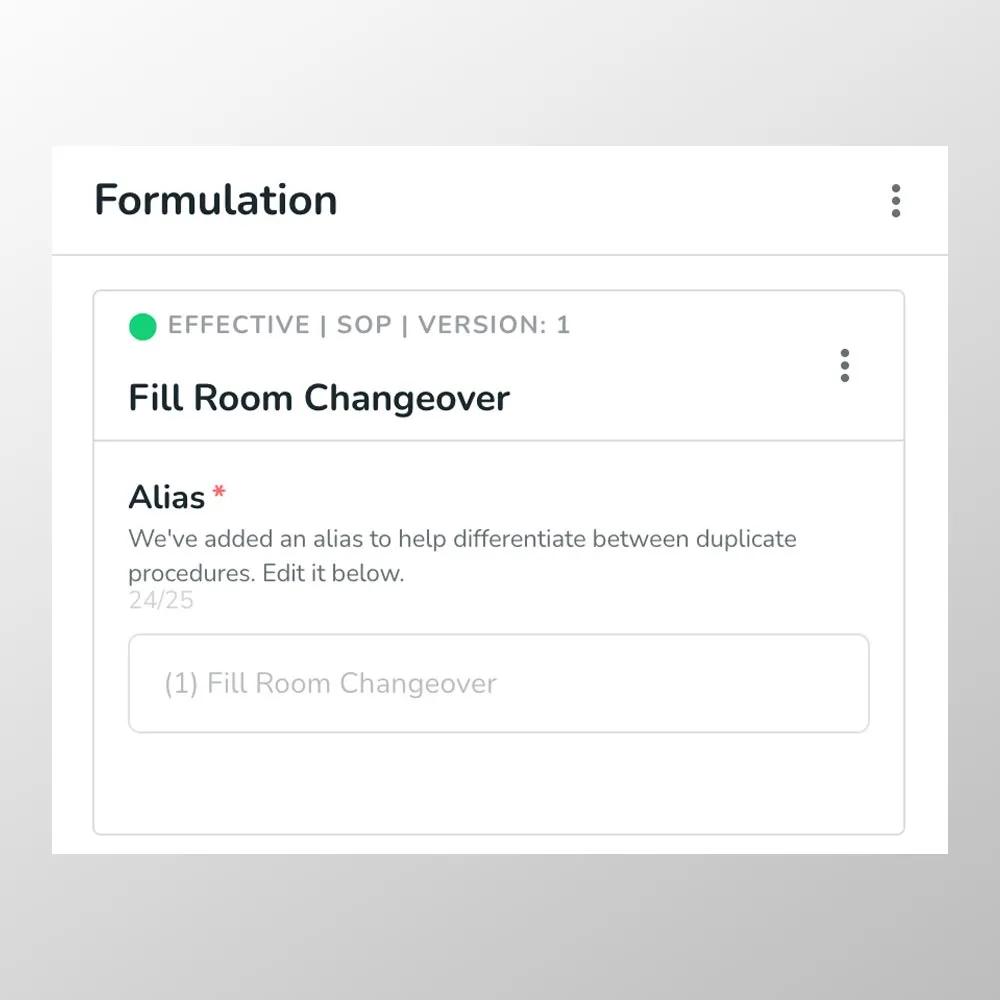
MANUFACTURE STAGE: USE CASE #1
Preparation and Staging
Execute all the other steps/procedures needed to prepare & stage a batch.
Set the foundation for the entire production process by carrying out all necessary procedures and steps essential for the accurate preparation and staging of a batch.
Batch preparation specialists and staging coordinators work in tandem to execute all the requisite steps and procedures, ensuring each batch is prepped and staged in compliance with strict industry standards.
$
R.O.I.
First-year savings for a site of 25 operators:*
Small molecule
$292,879
$292,879
Large molecule
$157,883
$157,883
MANUFACTURE STAGE: USE CASE #2
Manufacturing Execution
Manufacture a batch on the floor & in-suite efficiently & reducing risk.
Streamline the manufacturing process with real-time data and analytics to monitor, control, and optimize production activities while greatly reducing the potential for human error, enhancing overall batch quality and safety.
Production operators and in-suite specialists execute every step with precision and efficiently manufacturing a batch on the production floor, ensuring optimal quality while minimizing risks.
$
R.O.I.
First-year savings for a site of 25 operators:*
Small molecule
$819,690
$819,690
Large molecule
$82,008
$82,008

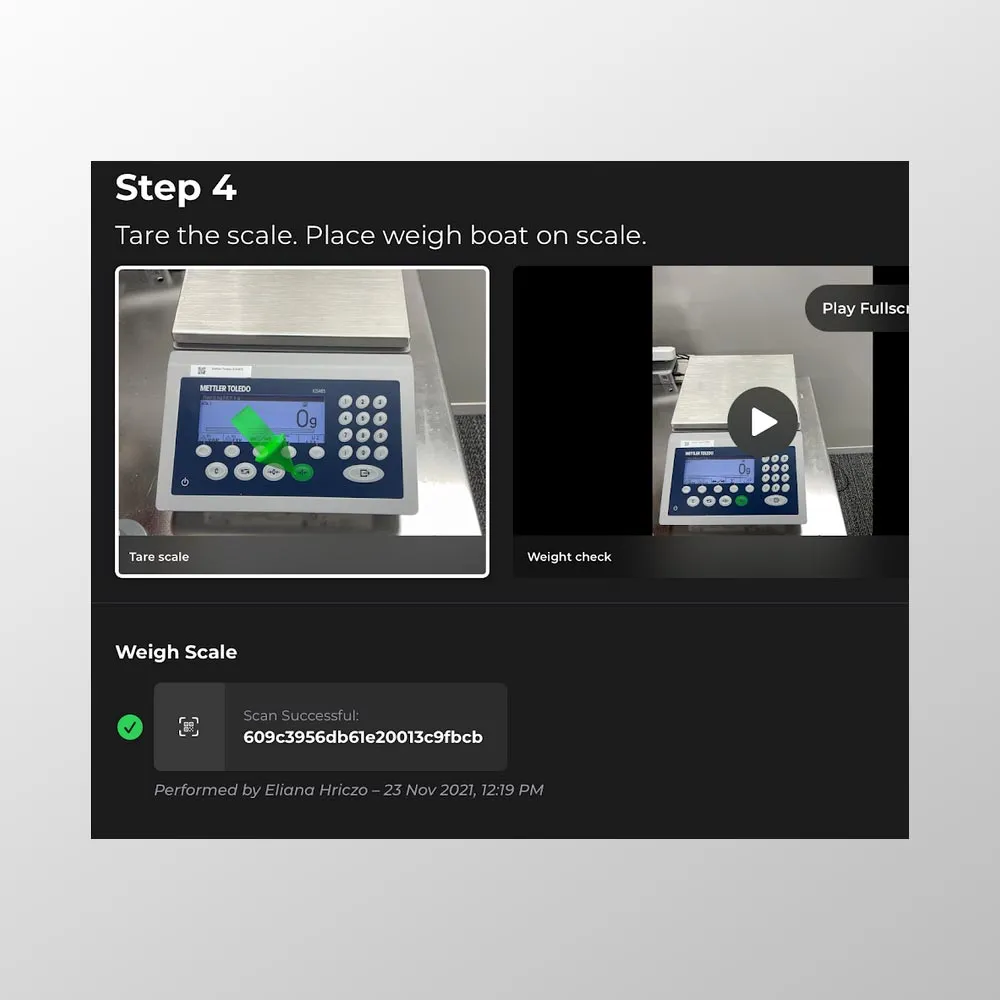
MANUFACTURE STAGE: USE CASE #3
Just-in-Time Training
Train in a quick and efficient manner using just-in-time guided & augmented training.
Swiftly equip personnel with the necessary knowledge right when they need it.
Production supervisors and training coordinators collaborate to deliver timely, guided, and augmented training sessions tailored to specific manufacturing tasks or equipment.
Enhance the training process with real-time insights, guided and interactive modules, and augmented visual aids, ensuring that the training is not only rapid but also comprehensive and contextually relevant.
$
R.O.I.
First-year savings for a site of 25 operators:*
Small molecule
$75,791
$75,791
Large molecule
$75,398
$75,398
MANUFACTURE STAGE: USE CASE #4
Logbooks
Conduct routine in-suite operations & batch support activities.
Systematically document and track of in-suite operations and batch support activities.
Aid the process with digital logbook functionalities that offer real-time data entry, automated error checks, and streamlined workflow integrations, ensuring accuracy and efficiency in recording essential manufacturing information.
Core personnel, such as in-suite technicians and batch quality analysts, routinely record data and observations to ensure transparency and compliance throughout the production process.
$
R.O.I.
First-year savings for a site of 25 operators:*
Small molecule
$39,270
$39,270
Large molecule
$3,927
$3,927
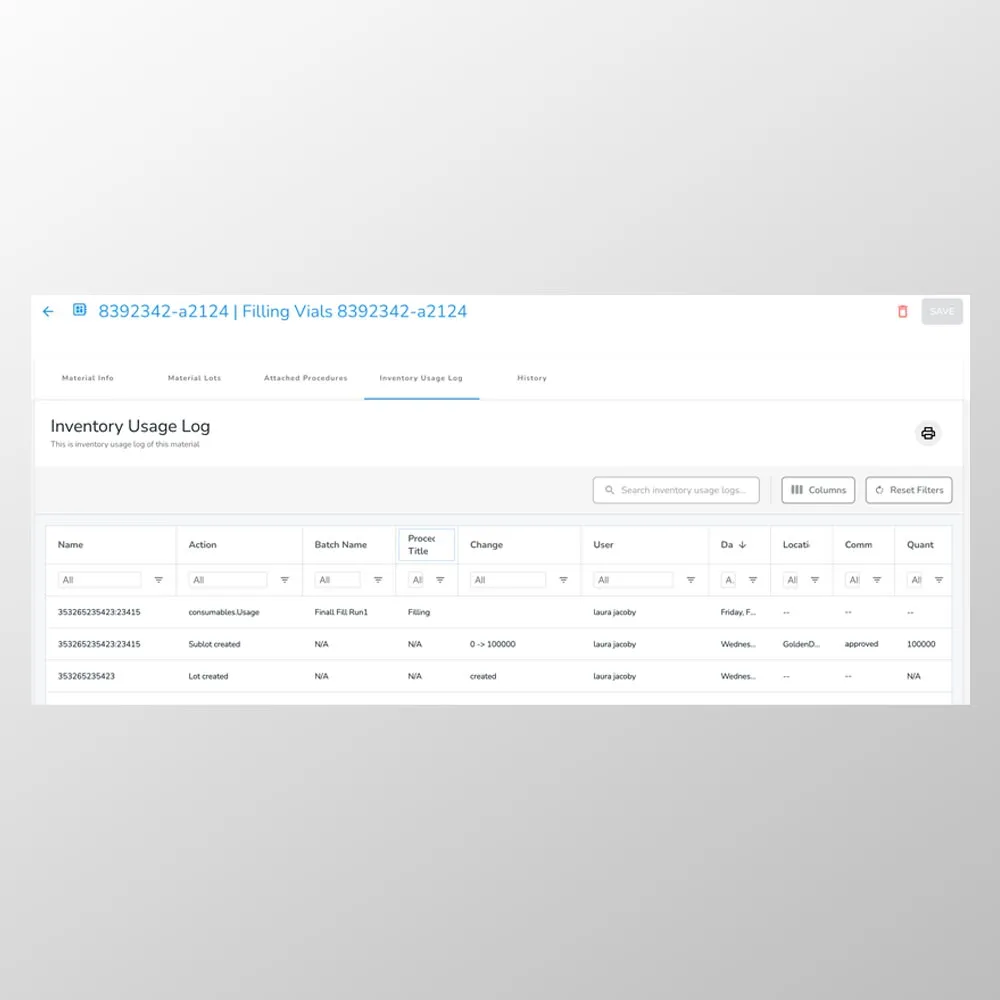
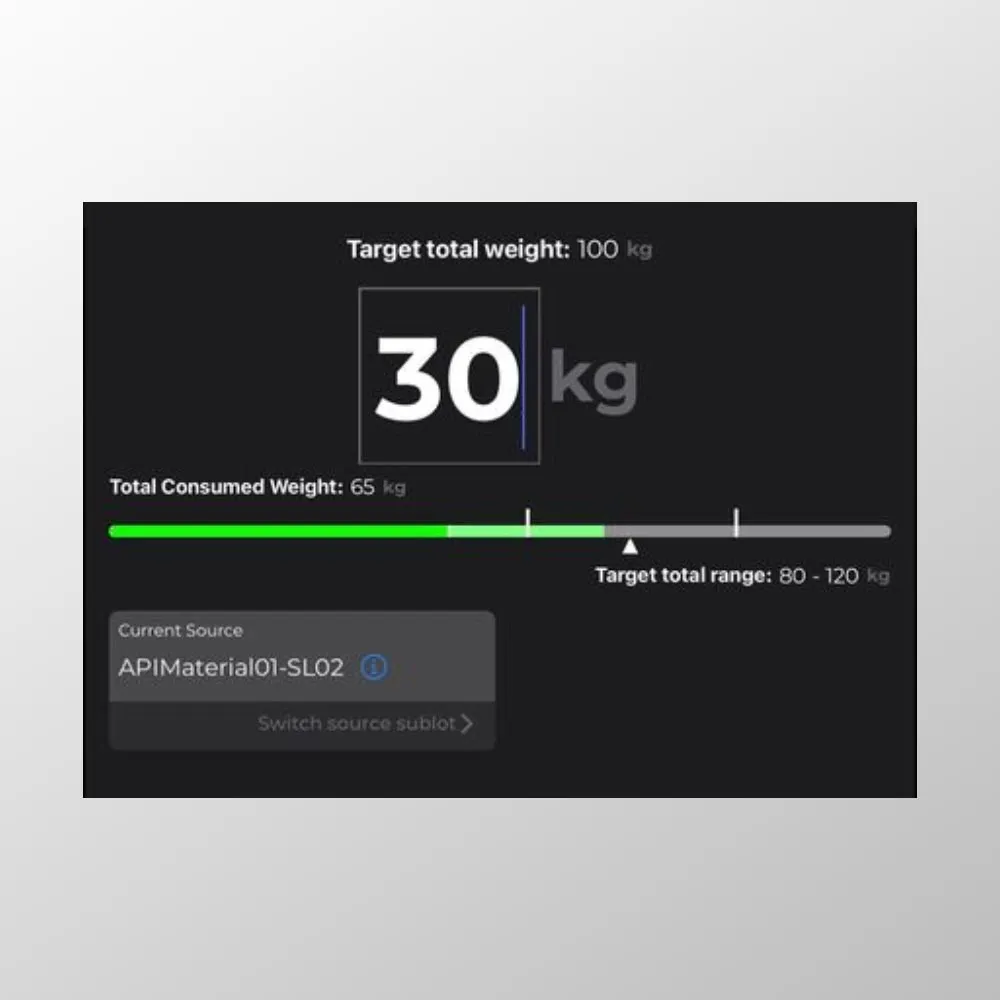
MANUFACTURE STAGE: USE CASE #5
Weigh, Dispense and Kit
Manage and execute work-in-progress inventory activities.
Manage the detailed procedures of measuring, allocating, and preparing materials for manufacturing.
Material handlers and dispensing technicians ensure the accurate weighing of raw ingredients, precise dispensing according to batch requirements, and systematic kitting for production stages.
Enhance these processes through automated weight checks, real-time material tracking, and streamlined kit assembly, guaranteeing efficiency, accuracy, and compliance.
$
R.O.I.
First-year savings for a site of 25 operators:*
Small molecule
$1,003,125
$1,003,125
Large molecule
$163,008
$163,008
MANUFACTURE STAGE: USE CASE #6
Remote Troubleshooting and Assistance
Enable operators and scientists to get help in real-time while on the shop floor.
Enable operators and scientists on the shop floor to instantly access expert assistance, ensuring they address issues promptly and maintain optimal production quality.
This real-time support not only enhances the efficiency of the manufacturing process but also empowers operators and scientists with timely insights, leading to improved decision-making and reduced downtime.
$
R.O.I.
First-year savings for a site of 25 operators:*
Small molecule
$122,703
$122,703
Large molecule
$61,352
$61,352
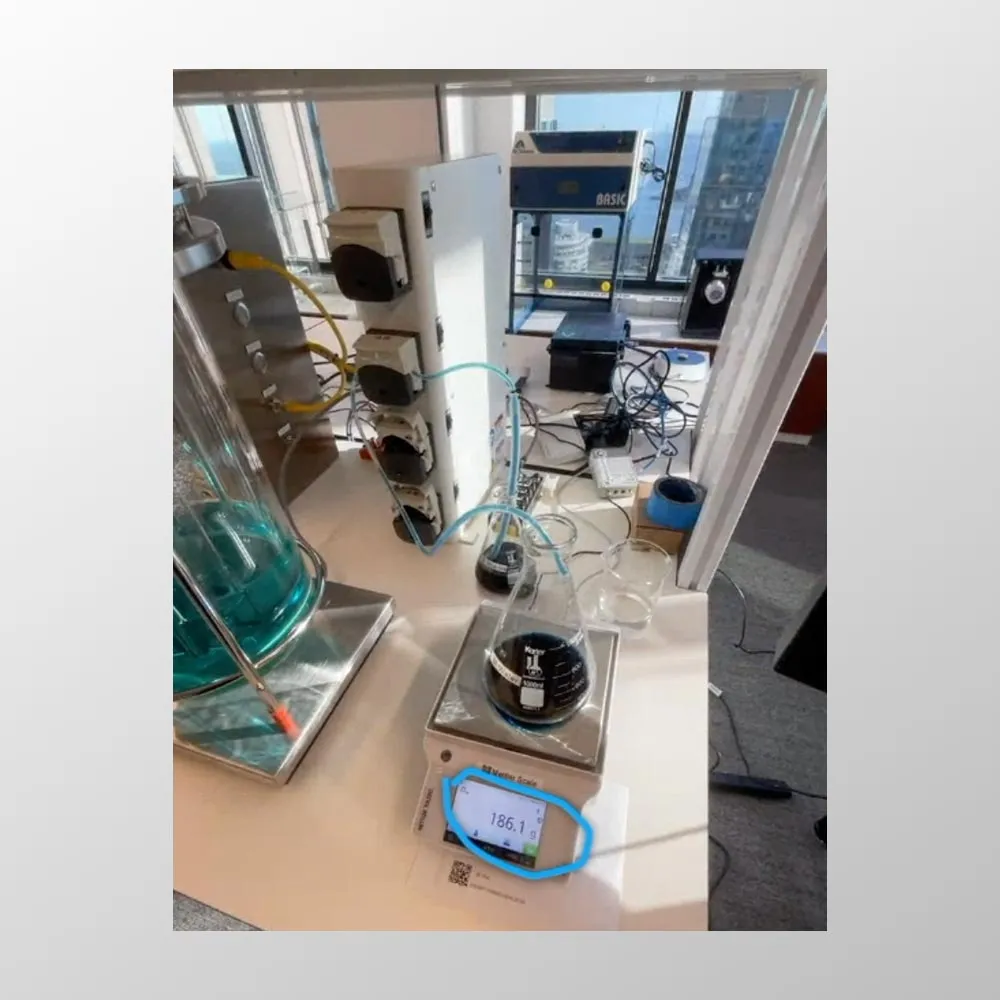
*ROI calculation assumptions — Small Molecule: Number of batch runs = 500; Payroll burden = 50%; Tech transfers to other sites using Tempo: 1. Large Molecule: Number of batch runs = 50; Payroll burden = 50%; Tech transfers to other sites using Tempo: 3.